Combiner des microstructures pour répondre aux contraintes physiques
La plupart des imprimantes 3D ne permettent d’utiliser qu’un seul matériau pour la création d’un objet. Or les propriétés mécaniques de ce matériau peuvent ne pas convenir au projet. Il est également possible que le projet nécessite des rigidités différentes selon les parties de l’objet, avec un extérieur plus dur par exemple.
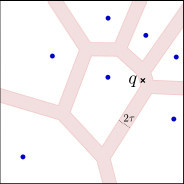
Pour répondre à ces problématiques, les chercheurs ont étudié comment mettre en place des microstructures pour répondre aux spécificités physiques attendues. Leur solution est de créer une mousse aléatoire, mais dont on puisse prédire les propriétés mécaniques. Pour cela ils ont utilisé l’homogénéisation, outil mathématique qui leur a permis de traduire en équations les attentes vis-à-vis de l’objet final, afin de pouvoir définir un matériau homogène « équivalent » à une mousse aléatoire. À partir de ce matériau équivalent (ou plusieurs si les densités varient dans l’objet), ils ont défini la structuration de la mousse en utilisant des diagrammes de Voronoï. En plaçant des « grains » dans l’espace en fonction des propriétés mécaniques attendues, les diagrammes créent des découpages appelés cellules tels que tous les points à l’intérieur d’une cellule sont plus proches de leur grain que de n’importe quel autre. Les arêtes du diagramme définissent ainsi les rayons de la mousse à imprimer.
Grâce à cet outil particulièrement flexible, les chercheurs ont défini une grille en fonction de l’élasticité voulue du matériau, en jouant sur le nombre de grains et l’épaisseur des arêtes imprimées par la machine. Cette méthode permet donc un ajustement très fin en fonction des besoins.
Il restait un dernier problème pour la génération de cette structure aléatoire. En effet, remplir un objet de 50 cm avec des éléments d’une épaisseur de 30 microns pourrait demander des capacités mémoire gigantesques. Pour résoudre cette problématique, les chercheurs se sont inspirés des techniques d’informatique graphique employés dans les jeux vidéo ou le cinéma. En effet, il arrive bien souvent qu’il soit nécessaire de représenter une planète compète, avec de nombreux détails. Pour pouvoir représenter cet espace, on utilise des méthodes de textures procédurales qui permettent d’attribuer une couleur à chaque point grâce à une fonction. En faisant apparaître tous les points, on obtient ainsi un rendu de matière complexe (comme le bois ou le marbre). Cela permet ainsi de générer à très faible coût de calcul des motifs riches. Les chercheurs ont étendu cette technique en passant du pixel au voxel, c’est-à-dire d’un carré d’image à un cube. En décrivant en tout point de l’espace si celui-ci est plein ou vide, il est possible d’avoir un ensemble cohérent et de charger au fur et à mesure dans la mémoire de l’imprimante 3D les tranches d’impression en cours de fabrication.
L’intérêt d’un tel apport est évident, pour permettre la création d’objets plus légers et tout aussi résistants, voire indéformables. Un projet concerne aussi une prothèse de doigt dont les phalanges ont une densité plus faible permettant la flexion, mais n’ayant pas besoin de structure mécanique. La création d’une mousse permet aussi d’exploiter les apports d’un milieu poreux qui est solide mais laisse passer des éléments comme l’air, l’eau ou même les cellules.
Publication : Procedural Voronoi Foams for Additive Manufacturing, de Jonàs Martínez [4], Jérémie Dumas [4] et Sylvain Lefebvre [4]
Voir aussi :